Recognizing Porosity in Welding: Checking Out Causes, Effects, and Avoidance Techniques
Porosity in welding is a persistent challenge that can considerably influence the high quality and integrity of welds. As experts in the welding industry are cognizant, recognizing the causes, results, and avoidance strategies connected to porosity is essential for accomplishing durable and trusted welds. By diving right into the source of porosity, examining its detrimental effects on weld quality, and discovering reliable avoidance techniques, welders can enhance their understanding and abilities to produce top notch welds consistently. The complex interaction of factors adding to porosity needs a comprehensive understanding and an aggressive strategy to make sure successful welding end results.
Common Reasons For Porosity
Porosity in welding is mainly triggered by a mix of factors such as contamination, incorrect securing, and inadequate gas protection throughout the welding procedure. Contamination, in the form of dirt, grease, or corrosion on the welding surface area, creates gas pockets when warmed, bring about porosity in the weld. Incorrect protecting occurs when the securing gas, frequently used in procedures like MIG and TIG welding, is not able to fully shield the liquified weld pool from responding with the surrounding air, causing gas entrapment and succeeding porosity. Additionally, poor gas insurance coverage, frequently as a result of incorrect circulation prices or nozzle positioning, can leave components of the weld vulnerable, enabling porosity to develop. These factors jointly add to the development of voids within the weld, weakening its stability and possibly creating structural issues. Recognizing and resolving these usual causes are essential steps in avoiding porosity and ensuring the high quality and toughness of welded joints.
Results on Weld Quality
The visibility of porosity in a weld can substantially endanger the total high quality and stability of the bonded joint. Porosity within a weld develops gaps or dental caries that deteriorate the framework, making it extra susceptible to breaking, rust, and mechanical failure. These spaces function as stress and anxiety concentrators, minimizing the load-bearing ability of the weld and boosting the likelihood of premature failure under used anxiety. In addition, porosity can also work as possible sites for hydrogen entrapment, further worsening the deterioration of the weld's mechanical properties.
Moreover, porosity can hinder the effectiveness of non-destructive screening (NDT) methods, making it challenging to spot other issues or stoppages within the weld. This can bring about considerable safety concerns, specifically in important applications where the structural integrity of the bonded components is paramount.
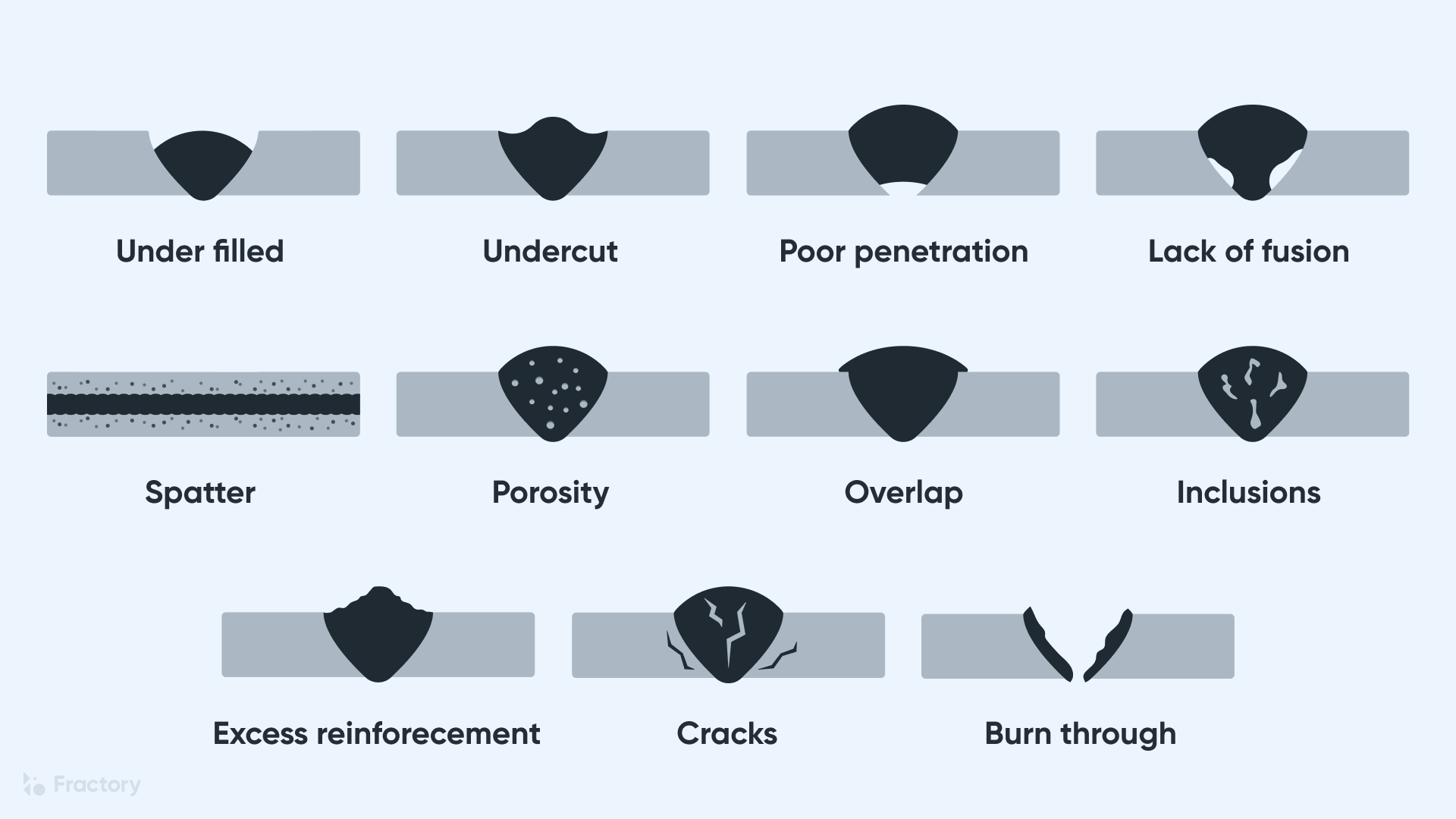
Prevention Techniques Overview
Offered the destructive influence of porosity on weld quality, effective avoidance strategies are crucial to maintaining the structural integrity of bonded joints. In addition, picking the ideal welding criteria, such as voltage, existing, and take a find out here trip speed, can assist reduce the risk of porosity formation. By incorporating these avoidance strategies right into welding methods, the incident of porosity can be considerably decreased, leading to stronger and extra trusted bonded joints.
Value of Appropriate Shielding
Proper securing in welding plays an essential role in protecting against atmospheric contamination and read making certain the honesty of bonded joints. Securing gases, such as argon, helium, or a mixture of both, are commonly utilized to protect the weld pool from responding with elements airborne like oxygen and nitrogen. When these reactive elements enter into contact with the hot weld swimming pool, they can create porosity, causing weak welds with lowered mechanical buildings.

Insufficient securing can cause numerous issues like porosity, spatter, and oxidation, endangering the structural stability of the bonded joint. Consequently, sticking to correct securing techniques is important to generate high-grade welds with minimal flaws and ensure the durability and dependability of the welded elements (What is Porosity).
Surveillance and Control Approaches
How can welders successfully check and manage the welding procedure to guarantee ideal outcomes and stop issues like porosity? By continuously keeping an eye on these variables, welders can recognize discrepancies from the ideal problems and make immediate adjustments to stop porosity development.

In addition, implementing appropriate training programs for welders is crucial for keeping track of and managing the welding procedure properly. What is Porosity. Enlightening welders on the relevance of maintaining consistent specifications, such as appropriate gas protecting and take a trip rate, can aid stop porosity issues. Routine analyses and qualifications can also ensure that welders are competent in tracking and managing welding processes
Additionally, using automated welding systems can improve tracking and control capacities. These systems can precisely regulate welding criteria, lowering the chance of human mistake and making certain consistent weld quality. By integrating sophisticated monitoring technologies, training programs, and automated click for more systems, welders can effectively monitor and regulate the welding process to minimize porosity problems and achieve high-quality welds.
Conclusion

Comments on “Recognizing What is Porosity in Welding: Causes and Solutions”